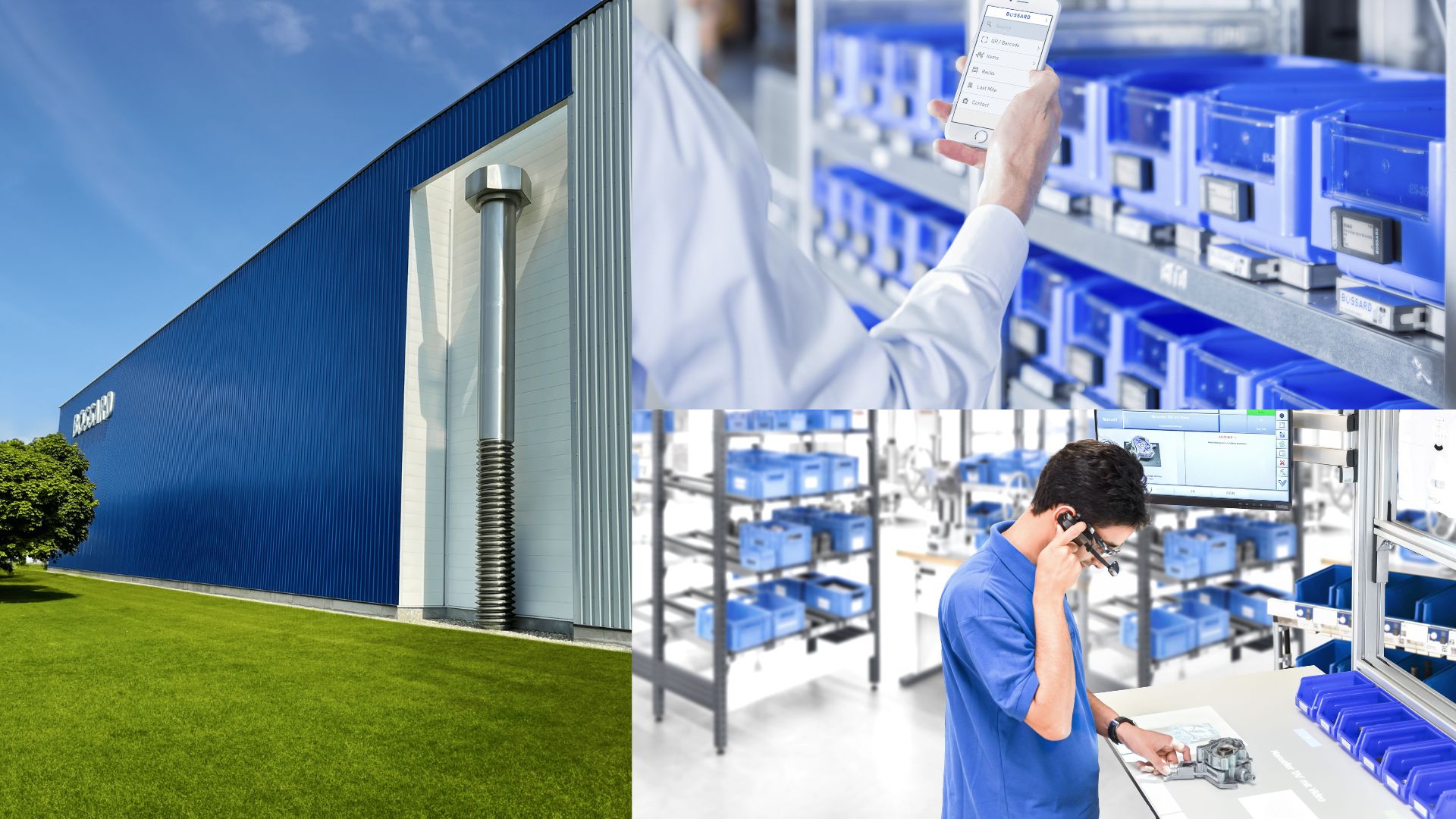
Bossard, France
Quelles sont les activités de Bossard ?
Le groupe, familial et de nationalité suisse, évolue dans le domaine des fixations industrielles et des techniques d’assemblage, pour la fourniture de produits et de services. Présent dans 33 pays et comptant un effectif d’environ 3.000 salariés, il est reconnu comme l’une des références mondiales de la spécialité. Nous cumulons plus d’un million d’articles proposés, depuis les petits de base (vis, rondelles, boulons) jusqu’à de complets ensembles complexes et nous proposons des prestations d’ingénierie associées.
Quel est le rôle de la filiale française au sein de cet ensemble ?
Bossard France est basée à Souffelweyersheim, au nord de Strasbourg et emploie près de 200 salariés, dont la moitié directement implantée au siège français. Nous faisons ainsi partie des plus importantes filiales du groupe à l’étranger. Nous assurons le stockage des produits, ainsi que les fonctions nécessaires en amont et en aval, de l’ingénierie à la vente. Souffelweyerheim présente aussi la particularité d’abriter un laboratoire d’essais et contrôle pour des tests de résistance, de comportement chimique, etc. Nous sommes des spécialistes des chaînes d’approvisionnement pour les différents secteurs industriels, avec comme cibles principales la robotique, l’automobile, le médical, ainsi que le ferroviaire et l’aéronautique. Le point d’évolution important concerne l’accompagnement de la numérisation dans l’entreprise : aujourd’hui tous les process se digitalisent et nous sommes tout à fait positionnés pour s’inscrire dans ce mouvement de fond.
Quel intérêt trouvez-vous à exposer à Be 5.0 – Industries du futur ?
En complément de Global Industrie et JEC World à Paris, nous recherchions, pour notre politique de présence à des salons, un rendez-vous de plus grande proximité géographique par rapport à nos bases française et internationale. Proche, ce salon l’est aussi de nos attentes : il rentre bien dans nos cibles, comme nous l’avons constaté dans le profil des visiteurs de notre stand l’an dernier où nous étions revenus exposer, après l’avoir fait lors de la toute première édition. Nous y avons enregistré de bons résultats en 2022.
Quelles solutions présenterez-vous plus particulièrement lors de cette édition ?
Nous mettrons en avant deux services. D’une part, Smart Factory Logistics, une solution d’optimisation de l’approvisionnement reposant sur un capteur de poids sur les bacs et un système de reconnaissance automatique de la demande : lorsque l’opérateur prélève une fixation, une détection automatique se déclenche pour transmettre au service logistique, par la combinaison de la radio fréquence et d’un réseau externe, l’information de reconstituer le stock et assurer le remplissage au bac, en vue d’une livraison directe sur le lieu d’utilisation.
D’autre part, nous ferons un focus sur Smart Factory Assembly. Il s’agit d’une solution de numérisation de l’assemblage qui apporte de nombreux soutiens aux opérateurs : choix du bon produit à monter au bon moment, traçabilité sur l’oubli éventuel d’une pièce, assistance pour parvenir au geste approprié, par exemple pour s’arrêter exactement au bon couple de serrage. Ce service diminue le temps de formation sans faire perdre à celle-ci sa qualité, elle aide à réduire la pénibilité de tâches.
Propos recueillis par Mathieu Noyer, rédacteur en chef de Traces Ecrites News, le site d’information économique du Grand Est et de la Bourgogne-Franche-Comté (www.tracesecritesnews.fr)